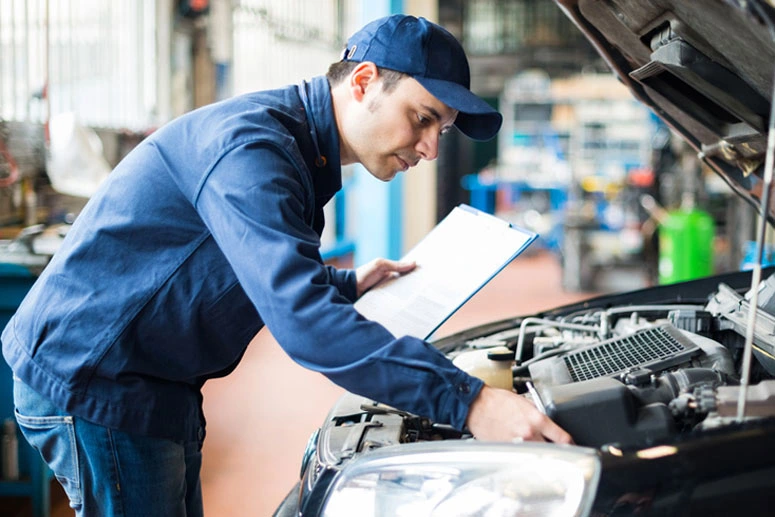
Le recyclage des batteries de voiture électrique représente un enjeu crucial pour l'avenir de la mobilité durable. Cet article explore les méthodes innovantes pour transformer ces composants essentiels en ressources durables, en mettant en lumière les défis techniques et les opportunités économiques qui accompagnent cette démarche écoresponsable.
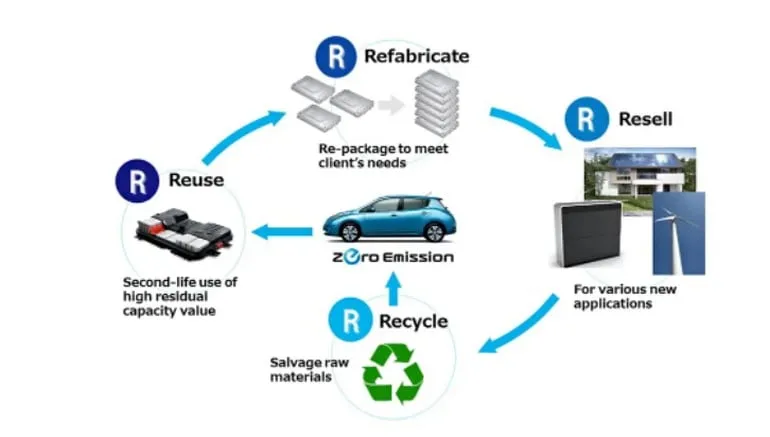
Processus de démantèlement des batteries lithium-ion pour véhicules électriques
Le démantèlement des batteries de voitures électriques est une étape cruciale du processus de recyclage. Cette opération complexe d'économie circulaire requiert une expertise pointue et des installations spécialisées. Le premier défi consiste à désactiver complètement la batterie pour éviter tout risque électrique. Une fois cette étape sécurisée accomplie, les techniciens procèdent au démontage minutieux des différents composants. La batterie est constituée de plusieurs modules, eux-mêmes composés de cellules individuelles. Ces éléments sont soigneusement séparés, permettant de récupérer les matériaux précieux tels que le lithium, le cobalt, le nickel et le cuivre. Le boîtier extérieur, généralement en aluminium ou en plastique, est également isolé pour être recyclé séparément. Une attention particulière est portée à la manipulation des électrolytes, substances potentiellement dangereuses qui nécessitent un traitement spécifique. Les circuits électroniques et les câblages sont également triés pour un recyclage adapté. Ce processus de démantèlement méticuleux permet d'optimiser la récupération des matériaux et la réutilisation des matériaux et de minimiser les déchets ultimes.Innovations récentes dans le recyclage des batteries : que peut-on attendre ?
Le recyclage des batteries de voitures électriques fait appel à des technologies de pointe, en constante évolution. Ces innovations visent à maximiser la récupération des matériaux stratégiques tout en réduisant l'impact environnemental du processus. Examinons les principales méthodes utilisées par les industriels du secteur.Hydrométallurgie pour l'extraction du lithium et du cobalt
L'hydrométallurgie est une technique particulièrement efficace pour extraire le lithium et le cobalt des batteries usagées. Ce procédé chimique utilise des solutions aqueuses pour dissoudre sélectivement les métaux d'intérêt. Les matériaux actifs des électrodes sont d'abord broyés finement, puis lixiviés dans des bains acides ou basiques. Des agents complexants sont ensuite ajoutés pour séparer les différents métaux. Cette méthode présente l'avantage d'être relativement peu énergivore et de permettre une récupération très pure des métaux. Elle est particulièrement adaptée au traitement des cathodes NMC (Nickel Manganèse Cobalt) et LCO (Lithium Cobalt Oxide) , largement utilisées dans l'industrie automobile.Pyrométallurgie et récupération des métaux précieux
La pyrométallurgie est une autre approche majeure du recyclage des batteries, particulièrement efficace pour la récupération des métaux précieux comme le cobalt et le nickel. Cette technique fait appel à des températures très élevées, souvent supérieures à 1000°C, pour fondre et séparer les différents composants. Dans un four à haute température, les matériaux des batteries sont transformés en un alliage métallique et une scorie. L'alliage, riche en métaux de valeur, est ensuite raffiné pour obtenir des métaux purs. Bien que ce procédé soit énergivore, il permet de traiter efficacement de grandes quantités de batteries et de récupérer une large gamme de métaux.Procédé mécanique de séparation des matériaux
Avant les traitements chimiques ou thermiques, les batteries passent généralement par une étape de séparation mécanique. Ce procédé vise à isoler les différents composants de la batterie sans altérer leur composition chimique. Les batteries sont d'abord broyées dans des conditions contrôlées, puis les matériaux sont séparés par des techniques de tri densimétrique, magnétique ou par courants de Foucault. Cette étape permet de récupérer des fractions relativement pures de cuivre, d'aluminium et de plastiques, qui peuvent être directement recyclées. Elle produit également une « black mass » , poudre noire contenant les métaux précieux, qui sera ensuite traitée par hydrométallurgie ou pyrométallurgie.Traitement électrochimique des électrolytes
Les électrolytes des batteries lithium-ion, composés de sels de lithium dissous dans des solvants organiques, représentent un défi particulier pour le recyclage. Des techniques électrochimiques innovantes sont développées pour traiter ces substances. L'électrodialyse, par exemple, permet de récupérer le lithium tout en décomposant les solvants organiques. Ces procédés émergents offrent la possibilité de valoriser des composants jusqu'alors considérés comme des déchets. Ils contribuent ainsi à améliorer le taux global de recyclage des batteries et à réduire leur impact environnemental.Enjeux économiques et environnementaux du recyclage
Le recyclage des batteries de voitures électriques ne se limite pas à un simple processus technique. Il s'inscrit dans une problématique plus large, englobant des enjeux économiques et environnementaux majeurs. Cette activité émergente cristallise les défis de l'économie circulaire appliquée à la mobilité électrique.Analyse du cycle de vie des batteries recyclées
L'analyse du cycle de vie (ACV) des batteries recyclées révèle des bénéfices environnementaux significatifs par rapport à la production de batteries à partir de matières premières vierges. Selon une étude récente, le recyclage permet de réduire les émissions de CO2 liées à la production de batteries de 50% à 70%. Cette diminution s'explique principalement par la réduction des activités extractives, très gourmandes en énergie et potentiellement polluantes. Cependant, l'ACV met également en lumière certains points d'attention. Le transport des batteries usagées vers les centres de recyclage peut avoir un impact non négligeable si les distances sont importantes. De même, certains procédés de recyclage, notamment la pyrométallurgie, consomment beaucoup d'énergie. L'optimisation de ces aspects est cruciale pour maximiser les bénéfices environnementaux du recyclage.Le recyclage des batteries n'est pas seulement une nécessité environnementale, c'est aussi une opportunité économique majeure pour l'Europe.
Réglementation européenne sur le recyclage des batteries (directive 2006/66/CE)
La réglementation européenne joue un rôle moteur dans le développement de la filière de recyclage des batteries. La Directive 2006/66/CE, récemment révisée, fixe des objectifs ambitieux en termes de collecte et de recyclage. D'ici 2025, 65% des batteries de voitures électriques devront être collectées, et ce taux passera à 70% en 2030. La législation impose également des taux minimaux de récupération des matériaux : 90% pour le cobalt, le cuivre et le nickel, 35% pour le lithium d'ici 2025, avec une augmentation progressive jusqu'à 70% en 2030. Ces exigences réglementaires stimulent l'innovation dans le secteur et encouragent les investissements dans de nouvelles capacités de recyclage.Marché émergent des matières premières secondaires
Le recyclage des batteries de voitures électriques ouvre la voie à un nouveau marché : celui des matières premières secondaires. Ces matériaux recyclés, particulièrement le lithium, le cobalt et le nickel, sont de plus en plus recherchés par les fabricants de batteries. Ils offrent une alternative aux ressources primaires, dont l'extraction est souvent controversée sur le plan environnemental et social. Selon les projections, le marché mondial des matériaux pour batteries recyclées pourrait atteindre 18,1 milliards de dollars d'ici 2030, avec un taux de croissance annuel de 8,5%. Cette dynamique crée de nouvelles opportunités économiques, notamment en Europe, où se développe une véritable industrie du recyclage des batteries.Acteurs majeurs et innovations dans l'industrie du recyclage
L'industrie du recyclage des batteries de voitures électriques connaît une effervescence sans précédent. De nouveaux acteurs émergent, tandis que des entreprises établies réorientent leurs activités vers ce secteur prometteur. Voici un aperçu des principaux acteurs et de leurs innovations marquantes.Redwood materials et son processus de recyclage en boucle fermée
Fondée par l'ancien directeur technique de Tesla, JB Straubel, Redwood Materials se positionne comme un pionnier du recyclage en boucle fermée. L'entreprise a développé un procédé innovant permettant de récupérer jusqu'à 95% des matériaux critiques des batteries. La particularité de leur approche réside dans l'intégration verticale : Redwood recycle les batteries et produit directement de nouveaux matériaux pour cathodes, prêts à être réutilisés dans la fabrication de nouvelles batteries. Cette approche circulaire réduit considérablement l'empreinte carbone de la production de batteries. Redwood Materials collabore déjà avec plusieurs constructeurs automobiles majeurs et prévoit d'étendre ses capacités de recyclage à 100 GWh de batteries par an d'ici 2025.Northvolt et son usine revolt ett en suède
L'entreprise suédoise Northvolt a fait sensation en annonçant la construction de Revolt Ett, la première usine de recyclage de batteries à grande échelle en Europe. Située à Skellefteå, en Suède, cette installation vise à recycler 125 000 tonnes de batteries par an, soit l'équivalent de 25 GWh de capacité de stockage. Northvolt se distingue par son engagement à utiliser 100% d'énergie renouvelable dans son processus de recyclage. L'entreprise a également développé une technologie propriétaire permettant de récupérer le graphite des anodes, un composant souvent négligé dans les processus de recyclage conventionnels.SNAM et sa technologie de recyclage hydrométrallurgique
La Société Nouvelle d'Affinage des Métaux (SNAM), basée en France, est un acteur historique du recyclage des batteries. L'entreprise a récemment investi dans une nouvelle ligne de traitement hydrométallurgique, spécialement conçue pour les batteries lithium-ion de véhicules électriques. Le procédé SNAM se distingue par sa flexibilité : il peut traiter différents types de batteries Li-ion sans nécessiter de tri préalable. Cette adaptabilité est un atout majeur face à la diversité croissante des technologies de batteries sur le marché. La SNAM vise à recycler 200 000 batteries de véhicules électriques par an d'ici 2030.Umicore et son approche intégrée du recyclage des batteries
Le groupe belge Umicore, leader mondial dans le recyclage des métaux précieux, a développé une approche intégrée du recyclage des batteries. Son usine de Hoboken combine des technologies de pyrométallurgie et d'hydrométallurgie pour maximiser la récupération des matériaux critiques. Umicore se distingue par sa capacité à produire des matériaux pour cathodes directement à partir de batteries recyclées. Cette intégration verticale permet de réduire considérablement l'empreinte carbone des nouvelles batteries. L'entreprise collabore étroitement avec plusieurs constructeurs automobiles pour développer des solutions de recyclage sur mesure.Défis techniques et perspectives d'avenir
Malgré les progrès significatifs réalisés ces dernières années, le recyclage des batteries de voitures électriques fait encore face à de nombreux défis techniques. Leur résolution est cruciale pour assurer la viabilité à long terme de la filière et optimiser son impact environnemental.Standardisation des designs de batteries pour faciliter le recyclage
L'un des principaux obstacles au recyclage efficace des batteries est la diversité des designs et des compositions chimiques. Chaque constructeur automobile développe ses propres technologies, ce qui complique le processus de démantèlement et de tri. Une standardisation des formats de batteries et de leurs composants faciliterait grandement le recyclage à grande échelle. Des initiatives émergent pour promouvoir cette standardisation. L'association européenne EUROBAT, par exemple, travaille sur des recommandations pour harmoniser les designs de batteries. Cette démarche pourrait non seulement améliorer l'efficacité du recyclage, mais aussi réduire les coûts de production et simplifier la maintenance des véhicules électriques.Développement de nouvelles chimies de batteries plus recyclables
La recherche s'oriente également vers le développement de nouvelles chimies de batteries intrinsèquement plus faciles à recycler. Les batteries LFP (Lithium Fer Phosphate) , par exemple, gagnent en popularité en partie grâce à leur recyclabilité accrue. Elles contiennent moins de métaux critiques et sont plus simples à démanteler. Des technologies prometteuses comme les batteriessolid-state
ou les accumulateurs sodium-ion pourraient également révolutionner le recyclage. Ces nouvelles chimies, en éliminant certains composants problématiques comme les électrolytes liquides, simplifient considérablement le processus de recyclage.
L'avenir du recyclage des batteries passe par une conception initiale pensée pour la fin de vie.
Automatisation et robotisation des processus de démantèlement
Le démantèlement des batteries reste une opération largement manuelle, ce qui limite la capacité de traitement et expose les travailleurs à des risques potentiels. L'automatisation et la robotisation de ces processus représentent un axe de développement majeur pour l'industrie. Des entreprises comme le suédois Stena Recycling investissent massivement dans le développement de systèmes robotisés capables de démonter rapidement et en toute sécurité les batteries usagées. Ces technologies s'appuient sur l'intelligence artificielle et la vision par ordinateur pour identifier les différents composants et adapter le processus de démontage en conséquence. L'automatisation promet non seulement d'accélérer le traitement des batteries en fin de vie, mais aussi d'améliorer la récupération des matériaux précieux. Des robots de tri avancés, utilisant des capteurs spectroscopiques, peuvent identifier et séparer les différents types de plastiques et de métaux avec une précision inégalée. Ces innovations technologiques sont essentielles pour faire face au volume croissant de batteries à recycler dans les années à venir. Elles permettront d'augmenter considérablement la capacité de traitement des usines de recyclage tout en réduisant les coûts opérationnels.L'automatisation du recyclage des batteries est la clé pour atteindre une véritable économie circulaire dans le secteur de la mobilité électrique.Alors que l'industrie du recyclage des batteries de voitures électriques continue d'évoluer rapidement, ces défis techniques stimulent l'innovation et ouvrent la voie à des solutions toujours plus efficaces et durables. La collaboration entre constructeurs automobiles, recycleurs et chercheurs sera cruciale pour relever ces défis et assurer un avenir véritablement circulaire pour la mobilité électrique. Comment imaginez-vous l'usine de recyclage de batteries du futur ? Sera-t-elle entièrement automatisée, gérée par des robots et des intelligences artificielles ? Ou bien l'expertise humaine restera-t-elle indispensable dans ce processus complexe ? La réponse se trouve probablement dans un subtil équilibre entre technologie de pointe et savoir-faire humain, permettant d'optimiser la récupération des matériaux tout en s'adaptant à l'évolution constante des technologies de batteries.
Développement de nouvelles chimies de batteries plus recyclables
La recherche sur les nouvelles chimies de batteries ne se limite pas à améliorer leurs performances ou leur densité énergétique. Elle vise également à concevoir des batteries intrinsèquement plus faciles à recycler. Cette approche, parfois appelée "design for recycling", est essentielle pour garantir la durabilité à long terme de la filière des véhicules électriques. Les batteries au lithium-fer-phosphate (LFP) gagnent en popularité, notamment grâce à leur recyclabilité accrue. Contrairement aux batteries NMC (nickel-manganèse-cobalt), elles ne contiennent pas de cobalt, un métal dont l'extraction pose des problèmes éthiques et environnementaux. Les batteries LFP sont plus simples à recycler et leurs composants sont plus faciles à séparer. D'autres technologies prometteuses sont en cours de développement. Les batteriessolid-state
, qui utilisent un électrolyte solide au lieu d'un liquide, pourraient révolutionner non seulement les performances des véhicules électriques, mais aussi leur recyclage. L'absence d'électrolyte liquide simplifie considérablement le processus de démantèlement et réduit les risques liés à la manipulation des batteries usagées.
Les accumulateurs sodium-ion représentent une autre piste intéressante. Utilisant le sodium, un élément beaucoup plus abondant et moins coûteux que le lithium, ces batteries pourraient offrir une alternative plus durable et plus facilement recyclable. Leur composition chimique plus simple facilite la séparation et la récupération des matériaux en fin de vie.
La conception de batteries pensées pour le recyclage dès leur création est la clé d'une véritable économie circulaire dans le secteur de la mobilité électrique.Ces avancées dans la chimie des batteries s'accompagnent de nouvelles approches dans leur conception physique. Des chercheurs travaillent sur des designs modulaires, permettant un remplacement facile des composants défectueux et un démontage simplifié en fin de vie. Cette approche pourrait considérablement prolonger la durée de vie des batteries et faciliter leur recyclage. Imaginez une batterie dont chaque module pourrait être remplacé individuellement, comme les pièces d'un jeu de construction. Non seulement cela réduirait les coûts de maintenance des véhicules électriques, mais cela simplifierait aussi grandement le processus de recyclage. Chaque composant pourrait être traité séparément, optimisant ainsi la récupération des matériaux. L'industrie fait face à un défi passionnant : comment concilier les exigences de performance, de sécurité et de recyclabilité dans la conception des batteries de demain ? La réponse à cette question façonnera l'avenir de la mobilité électrique et son impact environnemental à long terme.
Automatisation et robotisation des processus de démantèlement
L'automatisation et la robotisation des processus de démantèlement des batteries représentent une avancée majeure dans l'industrie du recyclage. Ces technologies promettent non seulement d'accroître l'efficacité et la capacité de traitement, mais aussi d'améliorer la sécurité des travailleurs et la précision de la récupération des matériaux. Des entreprises pionnières comme Stena Recycling ont développé des systèmes robotisés capables de démonter rapidement et précisément les batteries usagées. Ces robots, équipés de capteurs avancés et de bras articulés, peuvent identifier les différents composants d'une batterie et les séparer avec une précision chirurgicale. Cette approche réduit considérablement le risque d'exposition des travailleurs aux substances dangereuses et accélère le processus de démantèlement. L'intelligence artificielle joue un rôle crucial dans ces systèmes automatisés. Des algorithmes de vision par ordinateur analysent en temps réel la structure de chaque batterie, permettant au système de s'adapter à différents modèles et designs. Cette flexibilité est essentielle face à la diversité croissante des batteries sur le marché. Au-delà du démantèlement, l'automatisation s'étend également aux phases de tri et de séparation des matériaux. Des systèmes de tri optique avancés, utilisant des technologies comme la spectroscopie proche infrarouge, peuvent identifier et séparer différents types de plastiques et de métaux avec une précision inégalée. Cette étape est cruciale pour maximiser la pureté des matériaux récupérés et leur valeur sur le marché des matières premières secondaires. L'automatisation offre également des avantages en termes de traçabilité et de contrôle qualité. Chaque étape du processus peut être enregistrée et analysée, permettant une optimisation continue et une meilleure compréhension du cycle de vie des batteries. Cette transparence est particulièrement importante dans un contexte réglementaire de plus en plus exigeant.L'alliance de la robotique et de l'intelligence artificielle transforme le recyclage des batteries en un processus de haute technologie, ouvrant la voie à une véritable économie circulaire dans le secteur automobile.Cependant, l'automatisation soulève également des questions importantes. Quel sera l'impact sur l'emploi dans le secteur du recyclage ? Comment assurer une transition juste pour les travailleurs ? Il est crucial que le développement de ces technologies s'accompagne de programmes de formation et de reconversion pour les employés du secteur. Par ailleurs, l'investissement initial pour ces systèmes automatisés est considérable. Les petites et moyennes entreprises du secteur du recyclage pourront-elles suivre cette évolution technologique ? Des solutions collaboratives, comme des centres de recyclage partagés, pourraient émerger pour mutualiser ces investissements et rendre ces technologies accessibles à un plus grand nombre d'acteurs. L'automatisation du recyclage des batteries de voitures électriques n'en est qu'à ses débuts. À mesure que ces technologies mûrissent et se généralisent, elles joueront un rôle clé dans la réalisation des objectifs ambitieux de l'économie circulaire dans le secteur automobile. Elles permettront de traiter efficacement le volume croissant de batteries en fin de vie, tout en maximisant la récupération des matériaux précieux essentiels à la production de nouvelles batteries. Alors que nous entrons dans cette nouvelle ère du recyclage automatisé, une question se pose : comment l'industrie trouvera-t-elle le juste équilibre entre innovation technologique, responsabilité environnementale et considérations sociales ? La réponse à cette question façonnera non seulement l'avenir du recyclage des batteries, mais aussi celui de la mobilité durable dans son ensemble.